We use cookies to make your experience better. To comply with the new e-Privacy directive, we need to ask for your consent to set the cookies. Learn more.
Do I Need to Use Flux When Soldering? Understanding the Importance and Benefits of Flux
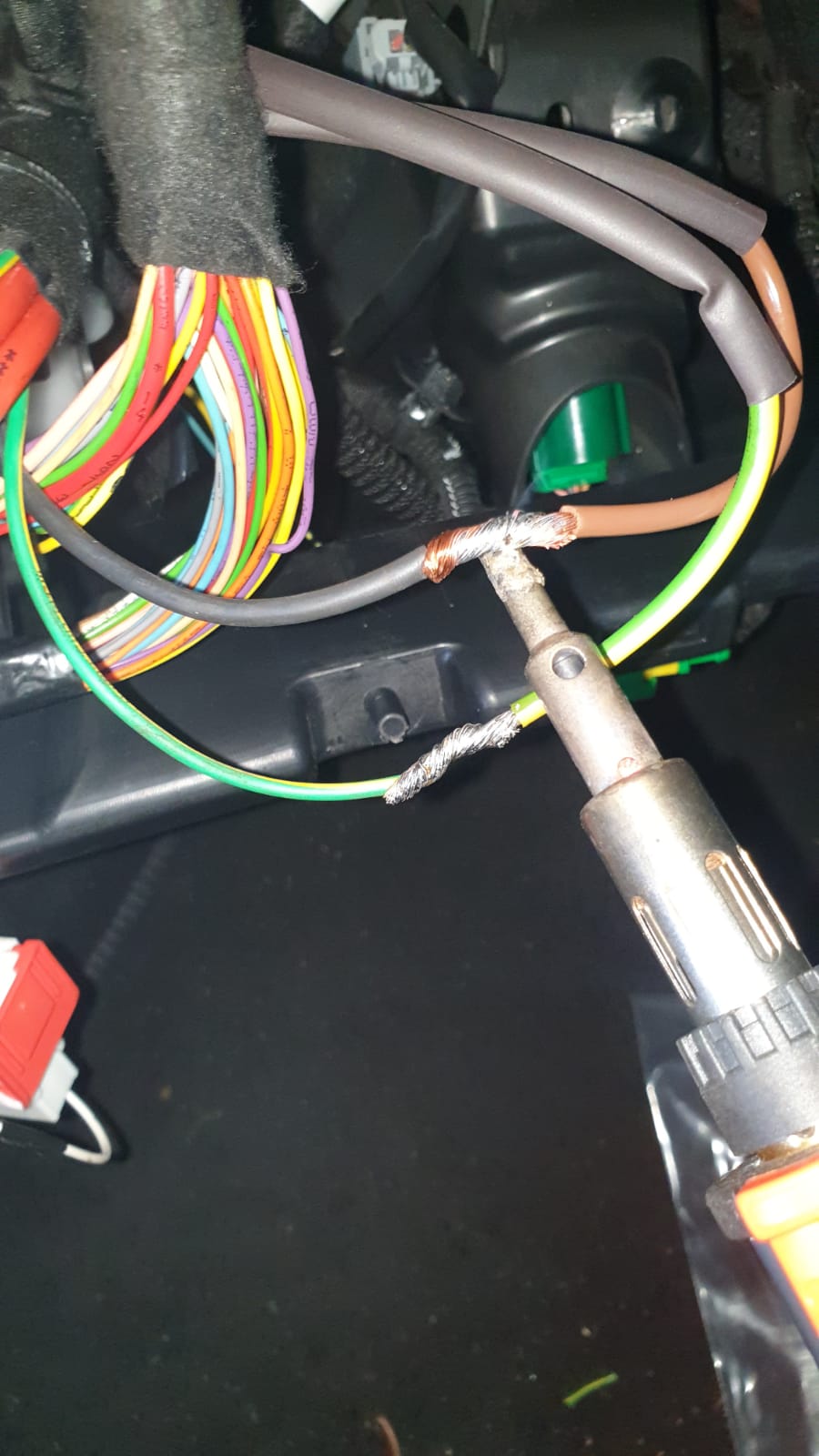
Soldering is a fundamental skill in electronics, plumbing, and various other industries. Whether you're a DIY enthusiast or a professional, you may have come across the term "flux" while soldering. But do you really need to use flux, and what does it do? In this article, we'll explore the reasons for using flux and its essential role in the soldering process.
What is Flux?
Flux is a chemical substance used in soldering to clean, prepare, and protect the surfaces to be joined. It comes in various forms, including paste, liquid, and core solder, and it typically contains a combination of chemicals such as rosin, organic acids, or inorganic compounds. Flux serves several critical functions during soldering, making it an indispensable part of the process.
Reasons for Using Flux:
1. Oxide Removal:
One of the primary functions of flux is to remove oxides from the surfaces to be soldered. When metals like copper, brass, or aluminum are exposed to air, they naturally form a layer of oxide. These oxides can hinder the solder's ability to bond with the metal, leading to weak or unreliable connections. Flux acts as a cleaning agent, breaking down these oxides and ensuring a clean surface for soldering.
2. Wetting:
Flux helps the solder "wet" the surface, which means it spreads evenly across the joint. Without flux, solder might bead up or form irregular shapes, making it challenging to create a strong and reliable connection. Proper wetting ensures that the solder adheres to the metal surface, creating a durable bond.
3. Solder Flow:
Flux also aids in controlling the flow of solder. It helps direct the solder to the desired areas of the joint, preventing it from flowing where it's not needed. This precision is crucial in soldering intricate or delicate components, as it minimizes the risk of shorts or solder bridges.
4. Preventing Reoxidation:
Even after oxide removal, metal surfaces can quickly reoxidize when exposed to air during the soldering process. Flux forms a protective barrier, preventing further oxidation while the soldering operation is underway. This ensures that the joint remains clean and free from contaminants during the critical soldering phase.
5. Improved Electrical Conductivity:
Flux can enhance the electrical conductivity of the joint. By ensuring a clean and even bond between the solder and the metal surfaces, flux helps maintain low resistance in electrical connections. This is especially crucial in electronics, where reliable electrical connections are essential.
Types of Flux:
There are different types of flux available, each designed for specific applications:
Rosin Flux: This type of flux is common in electronics soldering. It contains rosin, a natural resin derived from pine trees. Rosin flux is known for its excellent soldering properties and leaves a residue that is non-conductive and non-corrosive.
Water-Soluble Flux: Used in electronics manufacturing, water-soluble flux is easy to clean with water after soldering. It is essential for applications where post-soldering cleaning is required.
No-Clean Flux: As the name suggests, no-clean flux leaves behind minimal residue, making it suitable for applications where cleaning is not feasible or necessary.
Acid Flux: Typically used in plumbing, acid flux is more aggressive and designed for use on materials like copper pipes. However, it is not recommended for electronics due to its corrosive nature.
Conclusion:
In summary, using flux when soldering is not just a recommended practice; it is a critical step in achieving reliable, durable, and clean solder joints. Flux serves multiple purposes, including oxide removal, wetting, solder flow control, and preventing reoxidation. Choosing the right type of flux for your application is essential, as different flux formulations are suitable for different materials and requirements.
So, the next time you pick up a soldering iron, remember that flux is your trusty ally in creating strong and dependable connections. Embrace its power, and your soldering projects will benefit from cleaner, more efficient, and more reliable joints.